
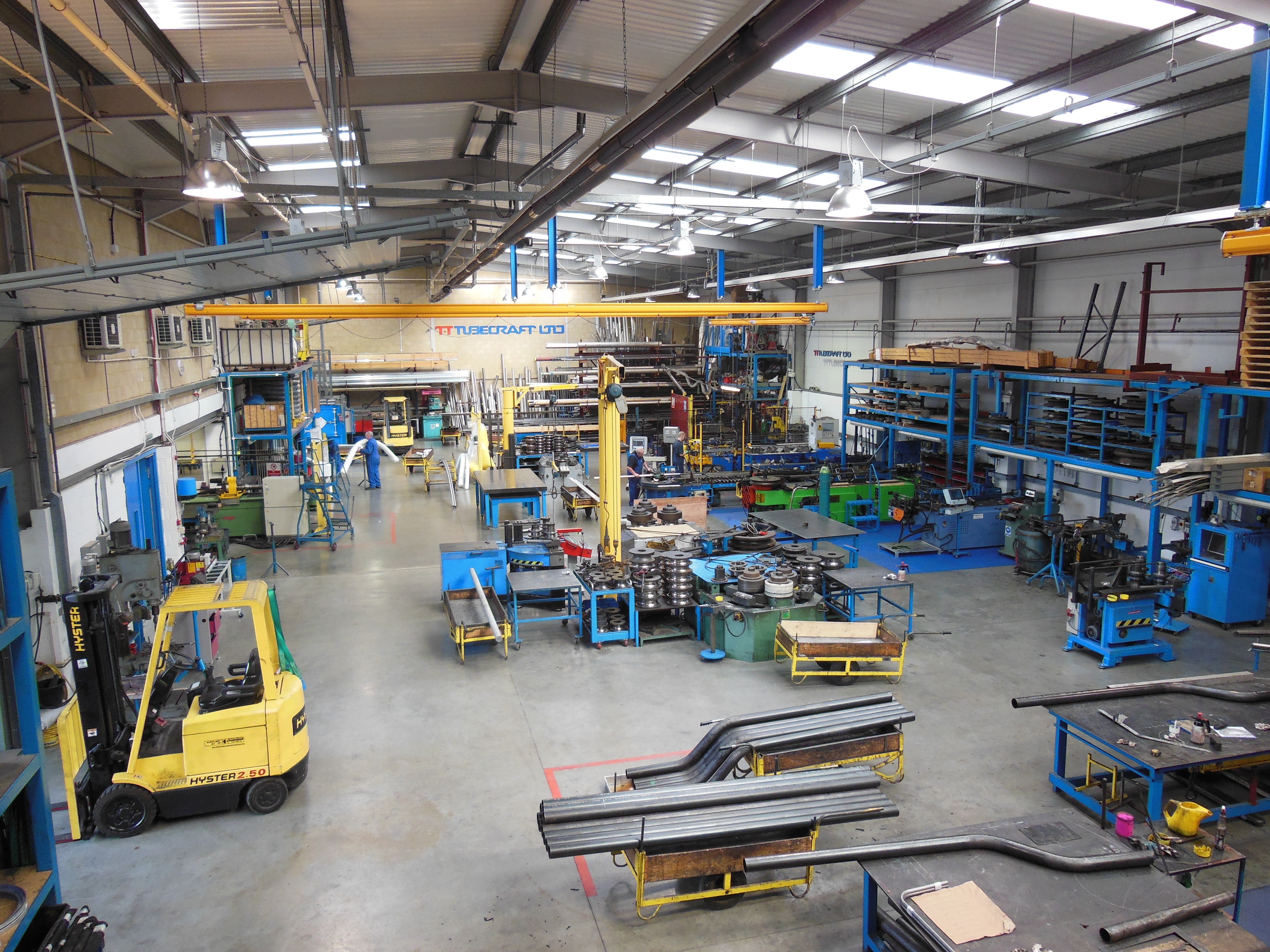
Straights between bends refers to a part that requires multiple bends. The degree of bend is the angle of the bend – measured on the outside. This can also be called the schedule in a pipe or the gauge in a tube. The wall thickness (W/T) is the measurement between the exterior and interior surfaces of the tube or pipe. The inside diameter (I/D) is the distance measured across the widest part of the inside opening of the tube or pipe. The outside diameter (O/D) is the distance across the widest area of the tube or pipe. The metal is formed into the bend design by the lower rollers pushing against the feed path. This allows it be shaped to a large centre line radius.
TUBE BENDING SPECIALISTS INC SERIES
A piece of tube or pipe is passed through a series of three rollers in a pyramid formation. Roll bending is used when large radius bends or curves are needed. It is the most commonly-used form of bending.

It is used in particular with thinner wall materials, as it helps to prevent defects – such as flattening, rippling or collapse – in the bend. Mandrel bending is carried out by placing a mandrel inside the pipe or tube that’s being bent. It does not involve the use of a mandrel. It involves the tube being clamped in place, while a pressure die moves around the radius to create a bend. Also called compression forming, this technique is the original method of bending tubes. An understanding of the terminology used within the tube and pipe bending industry will help you to better comprehend the basics:Ĭompression bending is a method of bending pipes or tubes when the die in place remains stationary, while a counter die is used to bend the material round the stationary die.
